May 6, 2021
Thousands of existing curb ramps are not ADA compliant.
This was largely due to loose guidance in the construction stage, conflicting requirements between design and construction, and tight metrics for judging compliance of the constructed ramp. For example, if a maximum landing slope 2.00% is required and constructed landing is measured at 2.01%, it is non-compliant.
As a result, agencies are spending tens of thousands of dollars per corner to replace these ramps.
As they rework curb ramps en masse–and seek to construct new ramps accurately the first time around–many agencies are running pilot programs to streamline design efforts in a way that’s compliant.
We’ve had the chance to work with several clients to use new tools and methods to design and deliver curb ramps. This list is by no means exhaustive, but here are three alternative delivery methods that have helped significantly cut down the time and cost of curb ramp design and construction, along with the unique advantages of each method.
Method 1: Preparing Designs on GIS Mapping
Portland Bureau of Transportation (PBOT) has developed an alternative curb ramp design method that utilizes the City of Portland’s extensive GIS mapping combined with in-field measurements by the design engineer (rather than a full-scale topographic survey). This method starts with setting a reference point or a Bench Mark using a PK nail with a relative set elevation in the curb about 30 feet outside the estimated limits of construction, making the design specific to that location where we collect data. Using a laser level at the intersection, the next step is to pull field measurements with a tape measure to key points of interest around the corner, and measure elevations to those points using the PK nail as the vertical reference point. The hand sketch effectively becomes the 30% concept layout.
We bring these hand sketched notes to the office to prepare the CAD design, check our work in the field again, then prepare a 60% design package. The City reviews this package, as well as the typical 95% and final submittal, then we prepare a final bid package that includes technical specifications, plans, and bid quantities for the contractor to bid. PBOT maintains an on-call roster of contractors for the curb ramp program so bidding and construction contracting is also streamlined.
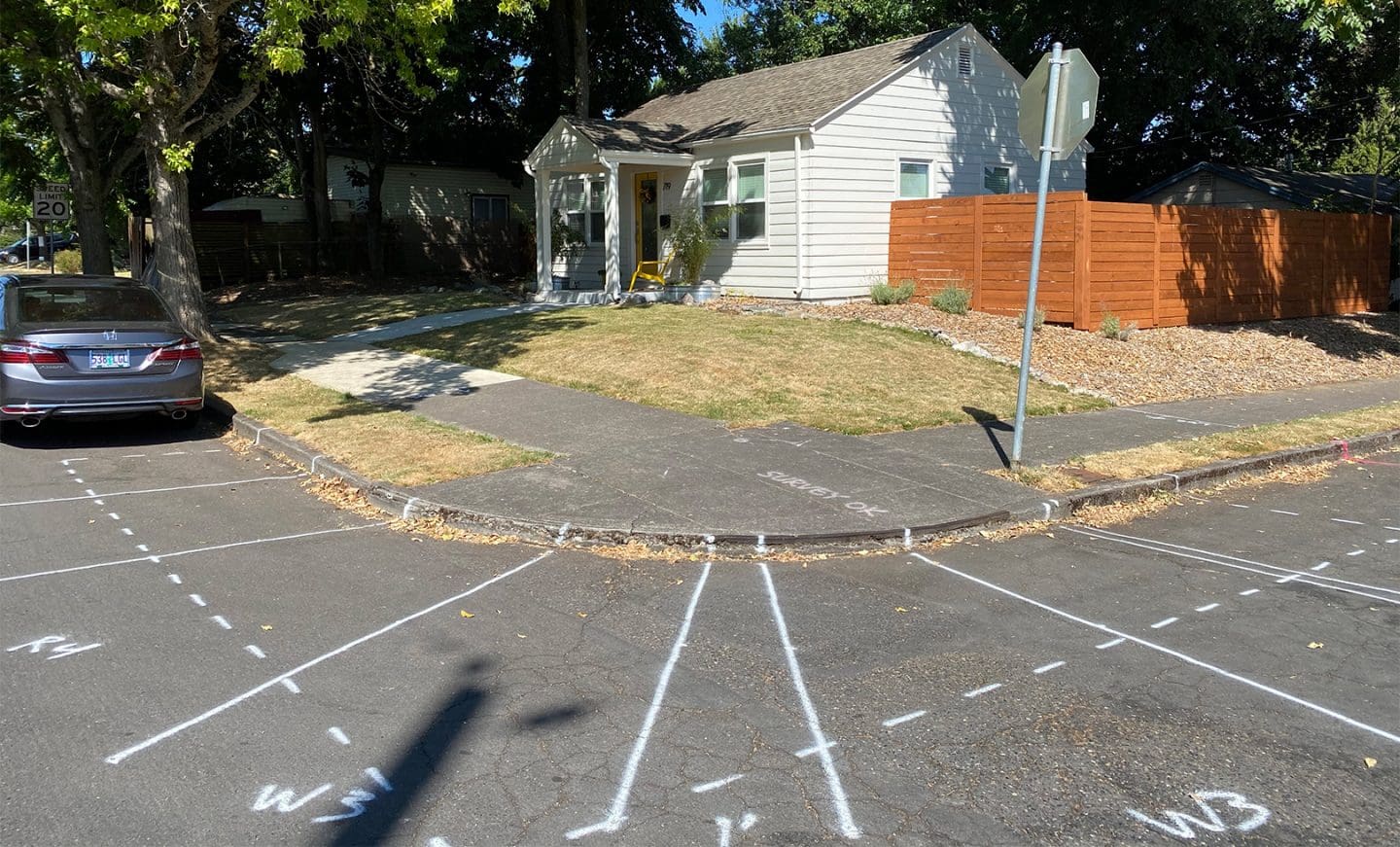
Photo credit: Nicholas Polenske and Eric Germundson
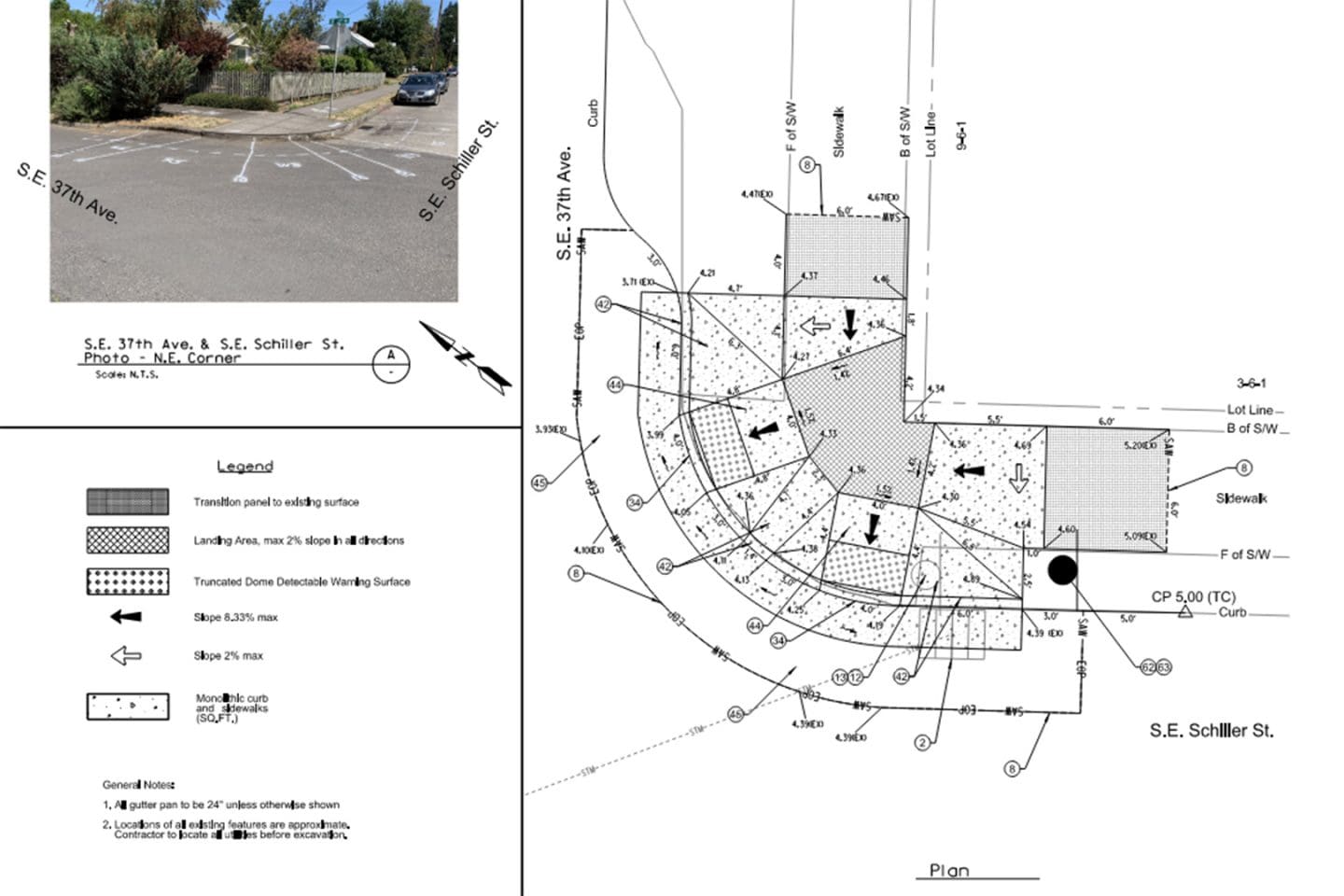
It is worth noting that this method is based on hand tape and laser level measurements in the field, which means there is room for error. As a result, tighter limitations for maximum slopes must be set in the design to afford for that error (for example, maximum ramp design slope is set to 6% instead of the typical 7.2% allowed by PBOT). This method is preferably used in areas with limited design challenges such as flat terrain, minor utility conflicts, and available right-of-way.
Advantages of This Method: This method gives the design engineer maximum control of layout and design, as they are involved from start to finish. In our work with PBOT, the person doing design is usually the construction manager as well which streamlines the process, significantly reducing the time frame compared to traditional delivery. It is also more affordable than having a full topographic survey done for multiple intersections.
Method 2: Rieker’s ADAM System
Specialized inspection tools can bring simplicity, accuracy, and speed to the process. In our work with PBOT, we’ve also used Rieker’s Advanced Data and Acquisition Measurement (ADAM) system, a forensic data acquisition tool that quickly measures curb ramps with National Institute of Standards and Technology (NIST) traceability. Though originally developed to be used in documenting ramp compliance, data collected by the tool can also be used for design.
Compared to the time and team size it takes to conduct a standard topographic survey, a tool like ADAM can be done with one person and the images can be set up on a local coordinate system with a reference point at data collection site. This tool uses 3D scanning technology that takes pictures at certain intervals and creates a point cloud so we can access elevation data associated with the isolated corner we’re designing. Similar to Method 1, this tool allows the civil engineer to collect the data and do the design so they are in control from beginning to end. (Note: Every state has different licensing laws for what constitutes engineering and land surveying and who can perform them, so check to be sure you’re within your jurisdiction.)
Advantages of This Method: When agencies have thousands of ramps to assess and replace, they need a way to move quickly without sacrificing accuracy. ADAM minimizes field time and allows us to use hard data for design. ADAM gives agencies a quick way to compile a database of existing condition information, keeping it at their fingertips, and we don’t have to use as tight of limitations on the design because the surface is a complete model. Similarly to the first method we described, this is a reduced cost and time frame compared to traditional delivery.
The data gathered using ADAM is another advantage to agencies trying to compile an inventory of their compliant/non-compliant curb ramps. While initially processing the data can be time-consuming, being able to quickly gather field data and having it at your fingertips to prioritize asset replacement is valuable.
Method 3: Close Coordination With Contractor
One of the primary reasons that curb ramps need to be reworked is the difficulty to convey the information developed during design through plans, and still allow for modifications in the field. Typically, design plans are produced independently of a contractor and then the winning contractor needs to recreate the design to suit their methods of construction. In Arizona, we’ve seen tremendous success partnering with the contractor during the design stage.
Our team in Tucson has teamed up with Granite Construction to understand the constraints they experience during construction, and design to those constraints, essentially rethinking the design process to accommodate the construction. We adapted how we use the software to design the curb ramp so that the output of the digital design directly matches the input of Granite’s automated machine guidance (AMG) excavator.
This process creates a symbiotic relationship between Kittelson and Granite that closes communication gaps. Without Granite, we would not know what exact data is needed. Without us, Granite would have to field fit during construction.
Advantages of This Method: This method mitigates the loss of information from design to construction through communication and digital delivery. Projects delivered in this way have come out under budget with no rework needed. The accuracy in the field is improved, and tolerances can be reduced.
Conclusion
Non-compliant curb ramps are a major equity and accessibility issue, and costing agencies across the country tens of thousands of dollars in rework. It’s important to invest the time and thought to try new methods for achieving ADA compliance in a streamlined and cost-effective fashion, and we’re excited to work with clients who feel the same. Feel free to contact us to talk through any of these methods in more detail.
P.S. Andrew Bailey and DJ Gregory recently published additional thoughts on improving compliance in ADA ramp construction through an idea they pitched as part of Kittelson’s Equity Challenge. Check it out here!